EXPANSION JOINTS FOR LNG/LPG CARRIERS
Once natural gas is extracted, it must be transported to different places to be processed, stored, and then finally delivered to the end consumer. Where natural gas cannot be delivered on land, it can be liquefied and delivered by ship. Compared to gas pipelines, liquefied natural gas (LNG) shipping is preferred for international transport because, in a liquid form, natural gas takes up less volume, making it easier for shipment and storage.
LNG infrastructure includes a gas pipeline leading to the seaside, gas liquefaction plant, storage facilities and an LNG terminal for shipment. After being liquified and transported to the area of demand, LNG is returned to gas form at regasification plants at the terminal.
A typical LNG carrier has four to six tanks located along the centerline of the vessel. Surrounding the tanks is a combination of ballast tanks, cofferdams and voids; in effect, this gives the vessel a double-hull type design. Inside each tank there are typically three submerged pumps. There are two main cargo pumps which are used in cargo discharge operations and a much smaller pump which is referred to as the spray pump. The spray pump is used for either pumping out liquid LNG to be used as fuel (via a vaporizer), or for cooling down cargo tanks.
EXPANSION JOINT DESIGN
Expansion joints are compensating elements for thermal expansion and relative movement in LPG/LNG carrier pipelines and engineered systems. This type of expansion joints have broad applicability and are used as:
• Hermetic sealing device for systems that convey high/cryogenic temperature substances such as LNG, steam or exhaust gases.
• Motion control to absorb movement and vibration.
• Dimension: DN 15-6000
• Design pressure: Up to 150 bar (de¬pending on the diameter and tem¬perature)
• Lifting capacity: Up to 16 ton
• Stainless steel, nickel alloy, aluminium, duplex, titanium.
CONSTRUCTION
Expansion Joints are the parts of pip¬ing system of pressurized equip¬ment. In this respect construction of the expansion joints are designed and produced according to European pressurized equipment directive (PED 2014/68/EU) as well as American Nation¬al Standard for piping process ASME Section VIII Div 1&2, ASME B 31.3.
All components of the expansion joints like, pipes, caps, flanges, tie rods etc… are checked by piping stress ana¬lysis thus enable us to se¬lect material type & thickness accord¬ing to permissible stress values
TEST&CERTIFICATION
• Expansion Joints are the parts of piping system of pressurized equipment in this respect construction of the expansion joints are designed and produced according to PED 2014/68/EU&ASME U Stamp-U2 Stamp.
• Expansion joints are exposed to hydrostatic pressure at 1,5 times of design pressure.
• For full vacuum applications, vacuum test at 760 Hg/mm is also applicable.
• Additionally, gas leakage detection with helium is advised for proper tightness.
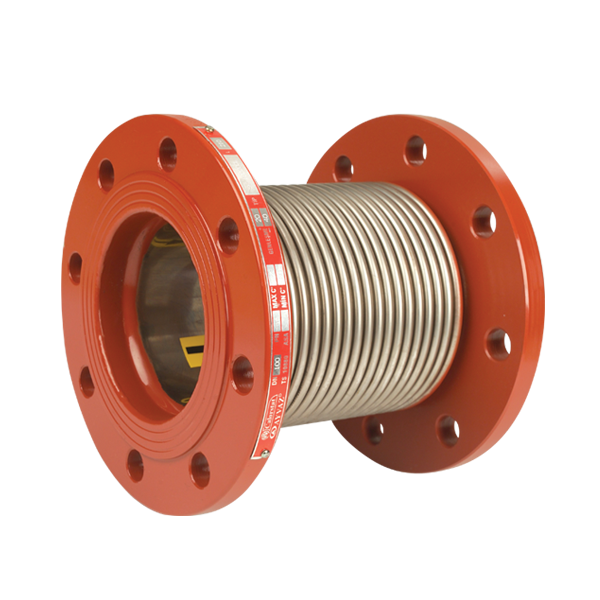
Inquiry Form
Please send us your inquiry using our contact form and we will contact you immediately.